TECHNOPOROUS ROLLER is a continuous, micro-porous foam roller based
on our original technology, excellent in various properties such as softness
resilience, water absorption and chemical resistance.
In addition, TECHNOPOROUS ROLLER is made of alternative base polymers
of polyolefin or polyurethane, so that the most suitable roller can be selected
for diverse uses each.
For example, a polyolefin roller is recommendable in a chemical resistance demanding
use, and so is a polyurethane roller in an abrasion resistance demanding use.
- Squeegee rollers/Minilabo,Printed circuit board,Lead-frame,Film, etc.
- Washing pads/Hard disc,Glass plate,wafer, etc.
- Coating rollers/Ink,oil,miscellaneous coating.
- Chemical squeeze rollers/Plating,Etching,etc.
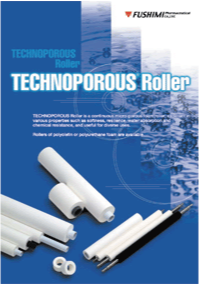
Material | U-16W | L-16W | L-26WH | |
---|---|---|---|---|
Polyurethane | Polyolefin | Polyolefin | ||
Apparent specific gravity | g/㎝3 | 0.24 | 0.25 | 0.26 |
Tensile strength | N/㎝2 | 67 | 39 | 41 |
Elongation | % | 300 | 480 | 230 |
Hardness | ASKER C | 10 | 9 | 18 |
Pore size | μm | 60 | 60 | 60 |
Heat resistance (Decay in water) | ℃ | 100 | 60 | 100 |
Water absorption | sec | Instant | Instant | Instant |
The above table is just for example. The properties are adjustable on demand.
- Outer diameter/Φ115mm or less.
- Thickness/38mm or less.
- Length/2500mm or less.
- Sizes larger than the above are available, as the case may be.
Retention % of tensile strength after 3 weeks immersion 25℃ |
TECHNOPOROUS U-26W | Competitor's polyurethane roller |
---|---|---|
Hydrochloric acid 10% | 100 | 99 |
Sulfuric acid 10% | 100 | 99 |
Sodium hydrate 10% | 63 | Decay in 4 days |
Chemicals | Tensile strength(Retention %) | Elongation(Retention %) | ||||||
---|---|---|---|---|---|---|---|---|
1 week later | 2 week later | 3 week later | 4 week later | 1 week later | 2 week later | 3 week later | 4 week later | |
10%Sulfuric acid | 102 | 100 | 100 | 101 | 100 | 102 | 99 | 101 |
47% Sulfuric acid | 101 | 96 | 100 | 107 | 95 | 105 | 95 | 93 |
60% Nitric acid 83 | 83 | 68 | 60 | 56 | 96 | 90 | 87 | 82 |
10% Hydrochloric acid | 100 | 100 | 99 | 101 | 101 | 99 | 103 | 102 |
36% Hydrochloric acid | 98 | 103 | 98 | 99 | 98 | 100 | 99 | 102 |
30% Acetic acid | 97 | 97 | 101 | 106 | 88 | 86 | 91 | 95 |
85% Phosphoric acid | 100 | 95 | 103 | 105 | 103 | 91 | 100 | 106 |
10% Sodium hydrate | 103 | 99 | 102 | 100 | 98 | 101 | 100 | 102 |
30% Sodium hydrate | 98 | 101 | 99 | 100 | 100 | 102 | 101 | 98 |
10% Ammonia | 102 | 92 | 97 | 106 | 100 | 104 | 103 | 96 |
10% Iron(Ⅲ)chloride | 103 | 100 | 101 | 102 | 101 | 99 | 103 | 101 |
40% Iron(Ⅲ)chloride | 106 | 100 | 99 | 102 | 98 | 93 | 97 | 96 |
30% Hydrogen peroxide | 98 | 96 | 98 | 106 | 94 | 102 | 100 | 103 |
Available chlorine 5% sodium hypochlorite | 100 | 97 | 102 | 103 | 98 | 104 | 101 | 98 |
5% Potassium permanganate | 101 | 106 | 99 | 94 | 102 | 98 | 88 | 68 |
Methanol | 99 | 99 | 100 | 101 | 102 | 98 | 100 | 100 |
Ethanol | 99 | 98 | 99 | 103 | 105 | 94 | 100 | 102 |
1.Retention %=Measured value/Original valuex100
2.The above measured values are not guaranteed.
3.Measurement is conducted at room Temperature.
Test method of chemical resistance
- 1. Sample size
- 60mm(L)X10mm(W)X2.5mm(T)
- 2. Immersion conditions
-
■ In PP container, the sample was submerged under the chemical solution volumetrically 20 times
or more the sample for each period.
■ Temperature 25±2°C.
■ After the submersion, the sample was washed with a large quantity of running water to eliminate remaining chemicals and dried. - 3. Tensile strength measurement
-
■ The two indication lines were put 20mm apart from each other on the lengthward center of the sample, and the measurement
was conducted by Tensile Strength Meter of Minebea Co., Ltd.
■ Tensile speed: 300mm/min.